Chaos at its best - Exciting Excursion for our international students
Did you ever wonder how Amazon is able to deliver every order so unbelievably fast? Last week, our international students went for an exciting excursion to discover the answer to this question: On a sunny Thursday morning we boarded a coach for a two-hour drive to Amazon’s Fulfillment Center in Rheinberg.
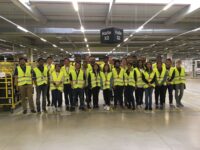
During a guided tour we gained interesting insights and were able to follow the different steps an item has to take to arrive at a satisfied customer: from the inbound to stowing where the articles are placed in coded slots, over the picking process, to the packing area before the package gets labeled automatically. From there, boxes are forwarded by destination and carrier – to get to the customer right on time.
For this purpose, there are 8 km of conveyor belts where 25.000 totes are being transported around 110,000 square meters of storage space filled with shelves up to 10 meters high. Up to 2 million different articles can be found here at times. These are dimensions one can hardly imagine – you just have to see it!
Given the large numbers one might expect a highly thought-out logistics management – but at first sight it seems rather chaotic instead. You can find unicorn money boxes next to body lotions next to fancy lamps. Numerous goods can be found doubled and tripled, scattered all over the place. It’s called “chaotic system” and it works surprisingly well – saving space and keeping walkways short ensuring every product arrives right on time. Disorder of this kind provides efficiency at a certain size – which was really impressive to see with your own eyes. More advanced warehouses even go a step further and eliminate the walking entirely having robots carrying product shelves to the pickers. In Rheinberg, items are currently put into the shelves by sight – which is a real sport during Christmas season, our tour guide explains with a wink.
At the end, our students took the chance to ask lots of questions regarding possible logistical issues or robotics enabling even more improvements. This opportunity was highly valued. Especially for our DDS students it was a great experience to see the results of software and algorithm utilization helping to optimize the complex systems implemented at Amazon. Overall, it was really amazing to experience a system of this size – seemingly chaotic but with the highest possible efficiency. An outstanding machinery gets started once you hit the confirmation button at the end of your order. And while you are sitting on your sofa looking for more items to shop, the one you just bought might already be on its way to your doorstep.
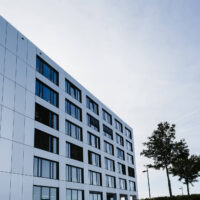